- Home
- Blog
- Print Work Column
- How to Calculate the Cost of Custom Teamwear? A Comprehensive Guide to Quotation Process
How to Calculate the Cost of Custom Teamwear? A Comprehensive Guide to Quotation Process
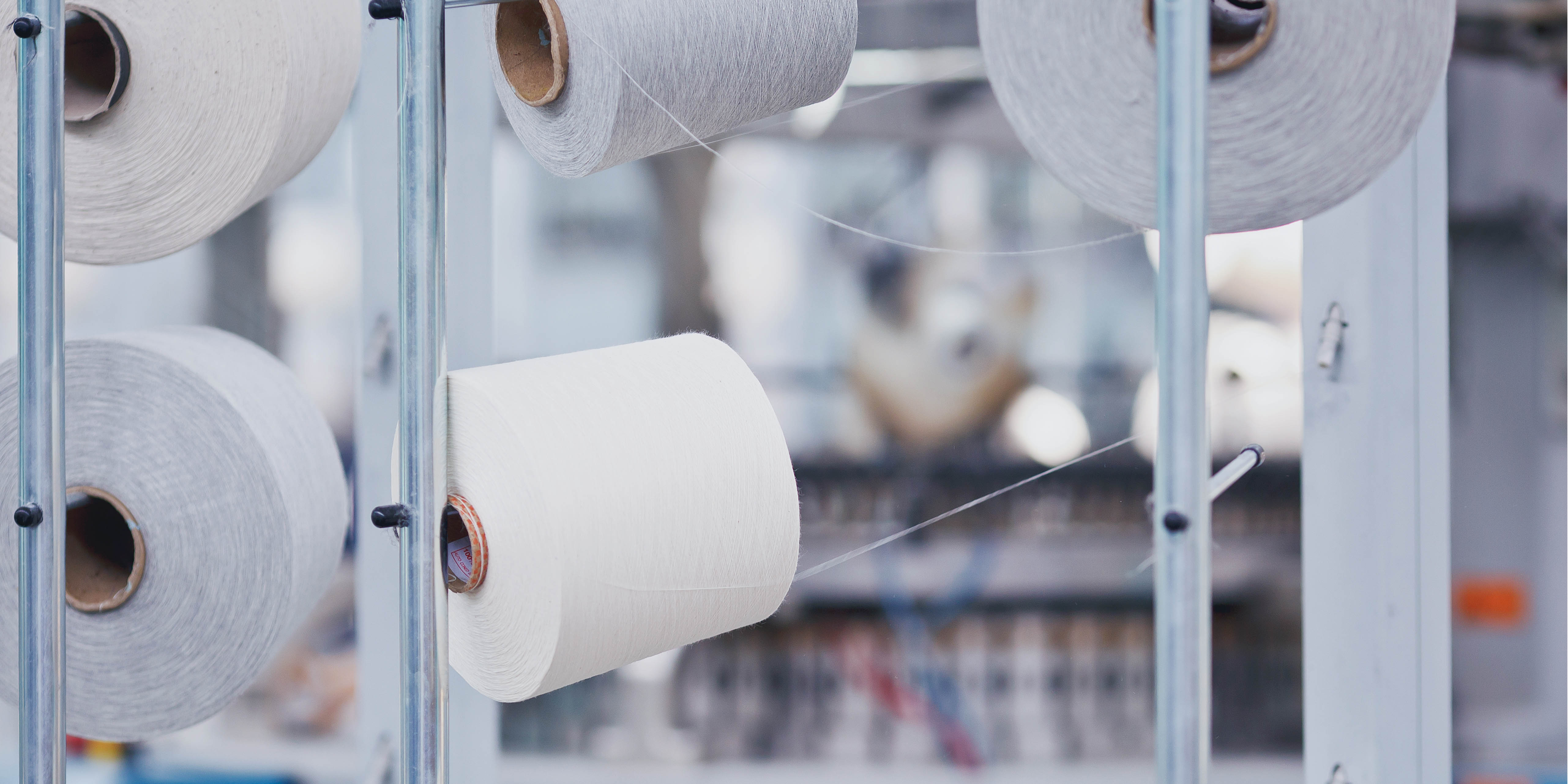
1. Basic Costs: Fabric and Style
The chosen fabric and style directly impact the base cost of teamwear. High-quality fabrics like cotton or polyester tend to be more expensive than lower-grade options. Additionally, the style of the teamwear, such as T-shirts, polo shirts, or hoodies, varies in cost. More complex styles naturally incur higher costs.
Basic costs include:
- Fabric types (e.g., cotton, polyester, blends)
- Style choices (T-shirts, polo shirts, long sleeves, etc.)
2. Printing and Design Costs
The printing technique significantly influences the overall cost of teamwear. Common methods like screen printing, heat transfer, and embroidery each have different costs and suitability. For instance, screen printing is ideal for large orders with lower per-piece costs, while heat transfer works well for smaller quantities or intricate designs but costs more per item.
Printing and design costs include:
- Printing methods (e.g., screen printing, heat transfer, embroidery)
- Design complexity (single-color or multi-color gradient designs)
- Design setup and file preparation (professional design services, if required)
3. Quantity
Quantity is a critical factor affecting cost. The unit price of teamwear typically decreases as order volume increases, as fixed costs for design and printing are distributed over a larger number of items. Bulk orders often qualify for discounts.
Quantity-related costs include:
- Order volume: Larger orders result in lower unit prices
- Impact of small orders: Smaller quantities may not benefit from bulk discounts
4. Delivery Time and Shipping Costs
Delivery time can also affect the quotation. Rush orders may require additional fees. Furthermore, shipping costs are a significant part of the final quote, especially for regional or international delivery.
Delivery time and shipping costs include:
- Rush order surcharges
- Shipping and logistics fees
5. Customization and Special Requirements
Special customization or additional design features, such as unique styles, extra pockets, or embroidery, will add to the cost. Ensure all special design requirements are clearly communicated before requesting a quote.
Special requirements costs include:
- Special designs (e.g., printing placement or custom areas)
- Additional customization options (e.g., pockets, zippers)
How to Obtain an Accurate Quote
To secure an accurate quote for custom teamwear, provide the following information:
- Quantity required
- Style and fabric choices (e.g., T-shirts, polo shirts, long sleeves)
- Printing method and design requirements (e.g., single-color or multi-color designs)
- Design files (AI/PS files for precise setup and cost calculation)
- Delivery time and shipping address
By clearly defining these requirements, you can obtain an accurate quote and calculate the total cost effectively.
Conclusion
Calculating the cost of custom teamwear requires a thorough understanding of factors such as fabric, design, quantity, printing techniques, and delivery time. Knowing the breakdown of each cost component helps you make informed decisions and secure the best deal. When you provide all necessary customization details, you can ensure an accurate quote and receive teamwear that meets your needs.
Article Classification
Recent Articles
- A Detailed Guide to the Custom Teamwear Process: From Order to Delivery
- How to Calculate the Cost of Custom Teamwear? A Comprehensive Guide to Quotation Process
- Introduction to Common T-Shirt Printing Techniques: Which One is Best for Your Needs?
- Color and Pattern Matching Tips for Team Apparel Design
- 5 Key Elements You Need to Know Before Customizing Team Apparel